Thursday, 5 October 202308:00 | Conference Registration, Materials Pick-Up, Coffee and Tea in the Exhibit Hall | | Session Title: Flow Chemistry Asia 2023 Opening Session |
| | | Session Chairperson: Professor Dr. Paul Watts, Nelson Mandela University |
| | 09:00 | 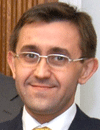 | Conference Chair Emerging Trends in Continuous Flow Chemistry Paul Watts, Distinguished Professor and Research Chair, Nelson Mandela University, South Africa
|
| 09:25 | 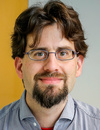 | Conference Chair Welcome and Introduction by Conference Co-Chairperson Simon Kuhn, Professor, Department of Chemical Engineering, KU Leuven Belgium, Belgium
|
| 09:30 | 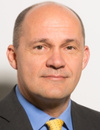 | Keynote Presentation Conference Opening Keynote -- Running Hazardous Chemistry in Flow – HF, F2, SF4 and More…… C. Oliver Kappe, Professor and Scientific Director, Center for Continuous Flow Synthesis and Processing, University of Graz, Austria
Organofluorine compounds are gaining popularity in chemical industries, especially in pharma and agrochemistry. Approximately 50% of the blockbuster drugs contain fluorine atoms. Organofluorine blockbuster drugs include e.g. atorvastatin (cardiovascular diseases), dolutegravir (HIV), emtricitabine (HIV), enzalutamide (cancer), and sitagliptin (diabetes). The introduction of fluorine atoms considerably influences the physical, chemical and biological properties of organic compounds as the bioavailability, lipophilicity or the metabolic stability of pharmaceuticals can be improved remarkably. This ever-increasing demand has transformed fluorine chemistry into a rapidly growing field of research. Despite this strong demand for fluorinated molecules in the pharma and agrochemical industry, the production of fluorinated compounds is often outsourced to specialized laboratories. This is likely the result of safety concerns in handling hazardous fluorinating reagents, alongside lack of expertise and equipment. Continuous flow chemistry has become an established method to perform hazardous reactions in a safe and controlled manner. In this lecture, contributions from our research group in the field of handling hazardous fluorinating reagents under flow conditions will be highlighted. Emphasis will be given on the safe use of HF (as amine complex), F2 (10% F2 in N2) and SF4 towards the synthesis of APIs or advanced intermediates. |
| 10:15 | 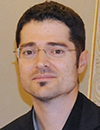 | Keynote Presentation Microfluidics, A Versatile Tool to Produce High Quality Nanomaterials in Continuous Flow Victor Sebastian, Full Professor, University of Zaragoza, Spain
In the last decade, the synthesis of nanomaterials with controlled size, shape and composition has received great interest due to their unique properties, enhancing their application in a plethora of fields: biomedicine, molecular diagnosis, biosensing, catalysis, energy, optics and electronics. Consequently, the controlled synthesis of nanomaterials has attracted significant attention because their properties are directly determined by their morphological and chemical features. However, there are urgent problems originated from very recent and practical demands in nanomaterial synthesis and the not straightforward scale-up of the successful laboratory-adapted protocols to an industrial level. This lecture will provide an overview of the adoption of microfluidic flow chemistry in the synthesis of inorganic, organic and hybrid nanomaterials. Microfluidics allows a novel process control window of well-defined nanomaterials, where the counterparts produced in conventional batch-type reactors are replicated but with an excellent control in size distribution, shape, and chemical composition. |
| 10:45 | Mid-Morning Coffee and Tea Break and Networking in the Exhibit Hall | 11:15 | Rapid and Column-Chromatography-Free Flow-Peptide Chain Elongation Shinichiro Fuse, Professor, Nagoya University, Japan
Peptides have become increasingly important as drugs. In this study, we developed rapid, mild and column-free peptide chain elongation via one-flow, three-component coupling approach using amino acid N-carboxy anhydride (NCA) which has both nucleophilicity and electrophilicity. The key to success was the rapid generation of acid chloride from amino acid and its rapid coupling with NCA via rapid dual activation. | 11:45 | Rapid Formation of Multi-layer Microcapsule in Microflow Takaichi Watanabe, Research Associate Professor, Okayama University, Japan
We present formation of multi-layer microcapsules using a simple emulsion drop formed in microflow. | 12:15 | 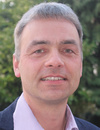 | Keynote Presentation New Opportunities for Flow Electrochemistry Thomas Wirth, Professor, Cardiff University, United Kingdom
The development of a microreactor for electrochemistry including applications to modern synthesis will be discussed. The electrochemical generation of hypervalent iodine compounds using this technique will be highlighted in detail, together with examples of halogenations using such reagents. Reactions towards the formation of N–N-bonds will also be discussed. |
| 12:45 | Networking Luncheon in the Exhibit Hall -- Network with Exhibitors, View Posters and Engage with Colleagues. **Lunch is Japanese Bento** | | Session Title: Engineering in Flow Chemistry, circa 2023 |
| | | Session Chairperson: Professor Dr. Simon Kuhn, KU Leuven |
| | 14:00 | 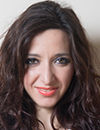 | Keynote Presentation Process Intensification: Producing More with Less Daria Camilla Boffito, Canada Research Chair in Engineering Process Intensification and Catalysis (EPIC) and Associate Professor, Polytechnique Montréal, Canada
Economic growth while accounting for social needs, climate change and environmental protection are key to tackle the United Nations Sustainable Development Goals (UN-SDGs) and accelerate the energy transition towards the electrification of the chemical industry. Green technologies based on cleaner energy sources such as biofuels, hydroelectricity, wind and natural gas are a global priority. Their implementation cannot only rely on existing industrial infrastructures but needs new resources and space. This represents a limit to the increase in the production capacity of existing chemical plants and to the development of new technologies. Process Intensification (PI) is a new archetype of the chemical industry that targets order of magnitude improvements to manufacture chemicals by either retooling existing facilities or finding new smaller, more efficient breakthrough technologies. Examples of PI technologies include HiGee reactors (e.g. spinning-disc reactors), alternative energy vectors to power chemical processes (ultrasound, microwaves, plasma), static mixers, and membrane reactors. In this talk, Prof. Boffito will show how PI still struggles to find a definition, despite the undisputable advantages. These include, for instance, energy, capital and operational expenditures (CapEx and OpEx) savings in the 20-80% range, and a reduction of emitted CO2 eq. up to 80%. She will also explain how PI represents a paradigm-shift that, by a matter of fact will change the chemical industry in the upcoming years. Prof. Boffito will browse the available methods to intensify chemical processes, specifically those for carbon capture and utilization (CCU), and will explain why we need to apply them both to existing and new processes. Further, she will highlight how PI can contribute to attain the UN-SDGs. |
| 14:30 | Sustainable Chemical Synthesis of High Added-Value Compounds from Renewable Sources in Flow Regime Julio Cezar Pastre, Associate Professor, University of Campinas – UNICAMP, Brazil
Raw materials from renewable sources, as well as agro-industrial waste, represent an attractive source of useful chemical functionalities. Our research group has already identified continuous flow processing as a fundamental technology for the valorization of such materials. Flow chemistry offers unique opportunities for the conversion of biomass derivatives into chemical compounds with higher-added value, since it brings numerous advantages in terms of unique process experience, scalability, and reduced environmental footprint. In this context, we will present our efforts for the synthesis of platform molecules (such as furanics) and new chemicals (monomers, nitrogenated aromatics) from biomass derivatives.
For some representative works, please see: Marçon, H. M.; Pastre, J. C. “Continuous flow Meerwein-Ponndorf-Verley reduction of HMF and Furfural using basic zirconium carbonate”. RSC Advances 2022, 12, 7980-7989.
Galaverna, R.; Fernandes, L. P.; Browne, D. L.; Pastre, J. C. “Continuous Flow Processing as a Tool for the Generation of Terpene-Derived Monomer Libraries”. Reac. Chem. Eng. 2019, 4, 362-367.
Galaverna, R.; Ribessi, R. L.; Rohwedder, J. J. R.; Pastre, J. C. “Coupling Continuous Flow Microreactors to MicroNIR Spectroscopy: Ultra-Compact Device for the Facile In-line Reaction Monitoring”. Org. Process Res. Dev. 2018, 22, 780-788.
Galaverna, R.; Breitkreitz, M. C.; Pastre, J. C. “Conversion of D-Fructose to 5-(Hydroxymethyl)furfural: Evaluating Batch and Continuous Flow conditions by Design of Experiments and In-line FT-IR Monitoring”. ACS Sustainable Chem. Eng. 2018, 6, 4220-4230. | 15:00 | Fundamentals and Research Progress of Photochemical Microreaction Technology Yuanhai Su, Professor, Shanghai Jiao Tong University, China
The research progress of our group in photochemical microreaction technology will be introduced, focusing on the design and construction strategies of photomicroreactors and its applications in synthesis of high-value chemicals associated with mass transfer, reaction kinetics and automatic control studies. | 15:30 | Mid-Afternoon Coffee and Tea Break and Networking in the Exhibit Hall | 16:00 | Contributions of Reaction Engineering Towards Efficient Photochemical Processes Dirk Ziegenbalg, Professor of Chemical Engineering, Ulm University, Germany
The contribution will discuss the fundamentals of photochemical reaction engineering in the context of comprehensive reporting and characterization of laboratory experimental setups. It will be shown that synergistic interdisciplinary work can lead to an enhanced photocatalytic performance through dynamic irradiation strategies, in-depth mechanistic understanding, and improved reactor designs. Examples will be provided to illustrate this point. | 16:30 | Green and Continuous Synthesis of Thiuram Disulfides via Electrochemical Microreactor Kai Wang, Associate Professor, Department of Chemical Engineering, Tsinghua University, China
Different kinds of thiuram disulfides was efficiently and environmentally synthesized with microreactors. | 17:00 | Process Intensification for the Electrification of Chemical Manufacturing Simon Kuhn, Professor, Department of Chemical Engineering, KU Leuven Belgium, Belgium
Small scale flow reactors have great advantages over conventional reactors, such as well-controlled flow patterns and increased surface-to-volume ratios, resulting in enhanced heat and mass transfer rates. Coupled with other benefits such as inherent safety allowing to perform reactions at elevated temperatures, pressures, or using highly reactive intermediates, they have become an attractive choice for the continuous manufacturing of chemicals and pharmaceuticals. However, these applications are still hindered by two important obstacles namely, weak convective mixing and issues regarding solids handling. Integrating ultrasound with small scale flow reactors has proven to be one of the more promising methods to address these issues. With selected examples, we will showcase the synergistic effect of ultrasound for particle synthesis, as well as electro- and photochemical processes. Exploiting these synergistic effects results in novel reactor concepts which will support the shift in chemical manufacture towards green and sustainable processes based on renewable energy sources. | 17:30 | Networking Reception in the Exhibit Hall with Japanese Beer and Sake | 18:30 | Close of Day 1 Conference Programming |
Friday, 6 October 202308:00 | Morning Coffee, Tea and Networking in the Exhibit Hall | | Session Title: Photochemistry and Other Approaches Converging with Flow Chemistry |
| | 09:00 | New Organic Electrosynthetic Processes Innovated by Flow Reactor Technology Mahito Atobe, Professor, Graduate School of Science and Engineering, Yokohama National University, Japan
Organic electrosynthesis is expected to be a typical green chemistry process because it does not require any hazardous reagents and produces less waste than conventional chemical synthesis. In fact, a number of successful new green organic electrolytic processes have been developed to date. In addition, electrochemical methodologies based on new concepts have been also developed. These related studies have become an active research area. This presentation will outline a new organic electrosynthetic processes based on flow reactor technology, focusing on our research. | 09:30 | Ultrafast and Continuous Flow Synthesis of Zeolites Toru Wakihara, Professor, The University of Tokyo, Japan
Zeolites have typically been synthesized via hydrothermal treatment, a process designed to artificially mimic the geological formation conditions of natural zeolites. This synthesis route, typically carried out in batch reactors like autoclaves, takes a time so long (typically, on the order of days) that the crystallization of zeolites had long been believed to be very slow in nature. Long periods of hydrothermal treatment also cause a burden on both energy efficiency and operational costs. Recently, we have reported the ultrafast syntheses of a class of industrially important zeolites within several minutes. Further shortening the crystallization time to the order of seconds would be a great challenge but can significantly benefit the mass product of zeolites as well as the fundamental understanding of the crystallization mechanism. | 10:00 | Pulse-Free/Continuous Flow Super Metering Pumps Harayuki Morikawa, General Manager, Fuji Techno Industries Corporation
In the introduction, we will explain the operating principles, performance, and benefits of our innovative products. The presentation will cover various applications and manufacturing equipment the pumps are used and the list of chemicals the pumps can handle. After that, the Pumping System with Versatile Controller will be presented.
| 10:30 | Mid-Morning Coffee and Tea Break and Networking in the Exhibit Hall | 11:15 | Sustainable and Scalable Flow Synthesis of Catalytic Colloidal Nanocrystals Noah Malmstadt, Professor, Mork Family Dept. of Chemical Engineering & Materials Science, University of Southern California, United States of America
New catalytic materials are central to addressing the current climate crisis. In particular, nanoscale crystals of metals as well as metal phosphides, carbides, and oxides are promising materials for upgrading biofuels and converting captured carbon dioxide. Industrial adoption of these materials has been limited by the energy intensive and difficult-to-scale solid-phase routes by which they’re typically synthesized. We are developing solution-phase routes to synthesize these materials as colloidal nanocrystals in millifluidic flow reactors. These routes minimize energy usage, allow for superior phase and size control of products, and facilitate scaling via millifluidic parallelization.
A general drawback to solution-phase synthesis is the cost of the solvent—in terms of economics, environmental risks, and heath hazards. To address this, we have been developing chemical routes to nanocrystal fabrication in sustainable ionic liquid solvents. Ionic liquids—organic salts that are molten at room temperature—have safety advantages due to their low volatility and non-flammability. They are also uniquely good solvents for nanocrystal fabrication due to their ability to stabilize early stage nuclei and to serve as weak surface ligands to growing nanocrystals. However, they are expensive—typically prohibitively so for industrial solvent applications. We have therefore developed actively controlled in-flow methods for recycling ionic liquid solvents used in nanocrystal synthesis. A techno-economic analysis of this recycling approach shows the recycled ionic liquid solvent cost is less than that of a typical volatile organic compound solvent. | 11:45 | 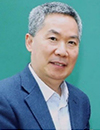 | Keynote Presentation Gas-liquid Micro Dispersion and its Performance Guangsheng Luo, Professor, Tsinghua University, China
Gas-liquid process is one of the most common multiphase processes in chemical industry, and the environmental-friendly, high-effective, safe technology is always a chasing goal. The gas-liquid microreaction technology provides a new opportunity for the intensification of the gas-liquid process, and good gas-liquid microdispersion is the prerequisite for the excellent performance of the subsequent reaction process. Accordingly, this report concentrates on the progress of gas-liquid microdispersion technologies from the development of the microdevice structure and the enhancement of the microdispersion performance. A strategy that changes the gas kinetic energy to generate the desired bubble/liquid slug size and gas-liquid flow regime is proposed to generate the Taylor bubble flow, bubbly flow, and short bubble flow. Besides, by embedding a capillary in the gas channel and introducing a step structure to the liquid channel, the bubble size can easily break through the restriction of microchannel size and can be reduced to 25% of the microchannel size, and the aspect ratio of the Taylor bubble can break through the critical value of 1.0 and be reduced to 0.5. Importantly, the mass transfer specific surface area in the novel gas-liquid microdispersion device is higher up to 10400 m2/m3 and the liquid-side mass transfer coefficient could be larger up to 60×10-4 m/s, which has increased by 30% and 5-9 times compared with the best level in the conventional T-junction microchannel, respectively. Finally, the direction of the gas-liquid microdispersion technology is pointed out. |
| 12:30 | Networking Luncheon in the Exhibit Hall -- Network with the Exhibitors, View Posters and Engage with Colleagues | | Session Title: Emerging Trends and New Advances in the Flow Chemistry Ecosystem |
| | 13:30 | 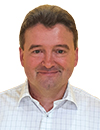 | Keynote Presentation Micro-Flow Resource Extraction: Marine Biomass, Minerals Processing, and Space Volker Hessel, Professor,, The University of Adelaide, Australia
The potential of micro-flow extraction has been investigated as early as microreactors have emerged, >30 years ago. Yet up to now no industrial use has been reported, despite the advantages being obvious, exploiting mass transfer as key advantage, and largely reported in literature. This is likely related to the fact that flow chemistry was and is largely driven by a market-pull principle from industrial side; mainly that of the pharmaceutical industry. The two potential industrial drivers in this presentation are either only cautiously testing the new frontier technology, mining industry, or are themselves a frontier market which is just developing, marine biomass market. Microreaction and flow technology has largely be developed in Europe, US, and some Asian countries; i.e. in zones that are typically poor in own resources, while resource-rich countries, in Australia, Africa, and South America, have been only slow adaptors of micro-flow technologies. This talk is given from the Australian perspective and market pull. A continent surrounded by huge ocean area has access to abundant marine biomass. The issue is to separate one compound selectively out of many dozens or even hundreds. As most marine biomass compounds are thermally labile, yet might profit from high-temperature extraction, the classical microreactor fortitude can be exploited – to do a processing job, impossible with current technology, in a very short time in a novel process window. For minerals processing, the ‘micro-flow job’ can follow manifold motivations. One is to extract all constituents (metals) from rich industrial (waste streams) and to concentrate it to a level that supports industrial post-processing. Another one is to selectively extract one metal in the presence of many others; both given for primary and waste streams. One more ‘job’ is to selectively remove several undesired compounds, leaving the right and wanted one in high purity. As these precious materials are typically given in low concentration, the extraction needs to be done at ppb-level. It will be shown how new functional materials with unseen properties can be designed via this ‘ultra-purity’. A third market with growing Australian relevance is space technology, and in the context of the presentation, lunar regolith simulant material is leached and extracted, to provide macronutrients (P, K) for plant growth in greenhouses on moon. |
| 14:00 | Mechanistic Origins of the Accelerated Hydrogenation in Flow Shusaku Asano, Assistant Professor, Kyushu University, Japan
Hydrogenation is a classical and well-studied reaction. However, there are many unexplained phenomena regarding its kinetics due to the complicated gas-liquid-solid interactions. I will introduce recent advances on this topic, especially in the flow system. | 14:30 | Continuous Flow Hydrogenations for the Chemical Manufacturing Industry Christian Hornung, Research Group Leader, CSIRO, Australia
Our group at CSIRO has developed a new structured catalyst reactor system, termed Catalytic Static Mixers or CSMs, which is based on 3D printed metal scaffolds coated with a noble metal catalyst such as Pt, Pd, Ni, Ru or others. These tubular reactors are used in continuous flow hydrogenations for the chemical manufacturing industry as well as for hydrogen reforming on demand. With the help of computational fluid dynamics, the structure of the mixer lattice can be optimised for a range of different outputs, such as minimised pressure drop, maximised heat transfer or optimised mixing. CSMs can be classified as a hierarchical catalyst system, whereby different length scales are addressed by different preparation methods; cm-, mm- and µm-scale features are formed by the 3D printing process and classical engineering design while certain µm- and nm-scale features are created during the catalyst preparation and deposition procedures. This results in a highly efficient and versatile catalyst platform which can be used in a broad range of different applications including homogeneous liquid phase, emulsion, liquid-gas and gas phase processes. | 15:00 | Continuous Aerobic Alcohol Oxidation in a Micro-Packed Bed Reactor with Nitroxyl-Radical Catalysts: From Homogeneous to Heterogeneous Jisong Zhang, Associate Professor, Tsinghua University , China
Selective aerobic oxidation is of crucial importance in organic synthesis, and sustainable oxidation strategies are highly desirable under green chemistry viewpoints. However, green oxidation processes rely not only on effective catalysts but also on the implementation of reactor technologies that enhance reaction performance and overall safety. Recently, nitroxyl radicals, as practical catalysts in oxidation have gradually attracted attention. These radicals can be further divided into stable radicals (such as 2, 2, 6, 6-tetramethylpiperidine nitrox, TEMPO) and active radicals (phthalimide-N-oxyl, PINO) produced by N-hydroxyimide (such as N-hydroxyphthalimide, NHPI). Nitroxyl radicals can form efficient catalytic systems in conjunction with metallic or non-metallic co-catalysts, enabling aerobic oxidations with high selectivity under mild conditions to obtain a variety of carbonyl compounds. Nevertheless, the existing nitroxyl-radical catalytic systems still face the challenges of high cost and limited recyclability. In this study, with a self-constructed micro-packed bed reactor platform, the space-time yields of alcohol oxidation to aldehyde and methylene oxidation to ketone were significantly enhanced by one to two orders of magnitude when compared to batch reactors. Furthermore, several novel strategies for nitroxyl-radical functionalized activated carbon catalysts are proposed, which not only surpass the state-of-art commercial silicon-based catalysts in terms of reactivity but also demonstrate exceptional stability in continuous-flow mode. | 15:30 | Break for Coffee and Networking in the Exhibit Hall. Please Bring Your Coffee to the Meeting Room for the Discussion that Follows | 16:00 | Discussion on Emerging Topics and Themes in Flow Chemistry -- Moderated by Conference Chairpersons: Professors Paul Watts and Simon Kuhn | 17:00 | Close of Conference |
|